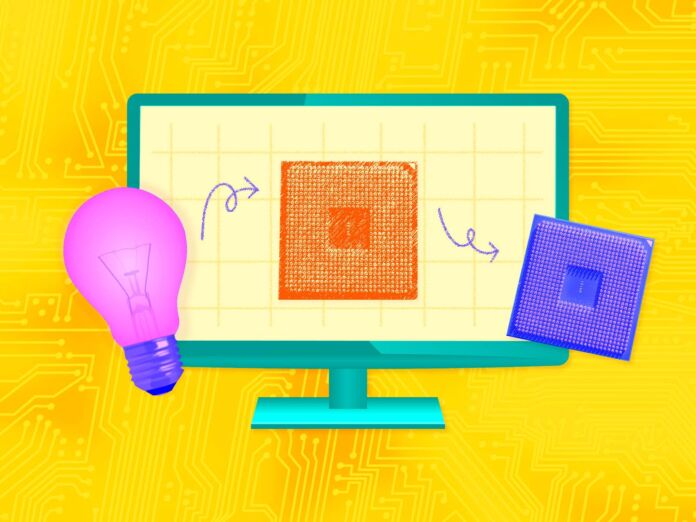
Getting a solid, innovative product to market faster than other companies gives you a distinct competitive advantage in markets ripe for disruption. (And what market isn’t ripe for disruption these days?) Sounds easy enough, but when it comes to IoT hardware development, how do you actually get that product out the door in the timeframe you need?
Increasing access to rapid prototyping techniques and tools now allows firms of any size to be competitive with well-established companies in multiple industries. With rapid prototyping techniques and tools advancing every day, implementing a rapid prototyping process is critical for elegant, efficient, robust, tested, and cost-effective product design.
What Is Rapid Prototyping for Agile IoT Development?
In a nutshell, rapid prototyping helps your mechanical engineers physically produce the part they just designed in a CAD software tool. This is typically done with a 3D printing or additive manufacturing process. Seeing a design come to life in a physical form really lets your engineers, product design teams, and users take a different look at the product, make revisions, and catch flaws.
What Kind of Rapid Prototyping Tool Should I Get For My IoT Hardware?
There are many different types of tools at varying price ranges, but they all do essentially the same thing and are becoming more and more cost-effective. Whichever one you choose for your IoT mechanical engineering project depends on your unique needs.
FDM
At the bottom of the price range, you have FDM (Fused Deposition Modeling) printers such as the Ender 3 or the Prusa i3. These types of printers have become very inexpensive but still produce an accurate representation of your design.
They use a plastic filament of your choosing that gets melted down and cooled into place in layers. FDM printing offers designers a wide selection of materials, from nylon, polycarbonate, and carbon fiber-strengthened filaments to flexible filaments like TPU. Taking advantage of this variety during early durability testing can save a tremendous amount of time and money before early manufacturing runs on your IoT project.
SLA
When it comes to SLA (Stereolithography) prints, these prints come out with exceptional quality and fit finish, although it’s worth noting that there are some drawbacks, such as an increased time to print, wash and cure times, and post-processing. These prints are an excellent way to prototype products in many different fields, especially products that have multiple curved surfaces.
When precise mechanical fitment and ingress protection are critical design parameters, SLA printing can pay for itself by identifying issues before moving on to injection molds. Here at Very, we utilize a Formlabs SLA printer with a variety of resins to achieve a very accurate and smooth finish for our clients’ prototypes.
SLS
On the higher end of price and performance, you have SLS (Selective Laser Sintering) printing. These printers typically use a bed of powder nylon and a laser to scan and sinter each cross-section. SLS printers are a bit faster than SLA but usually have a slightly rough finish because of the powder used for printing.
Perhaps the most unique feature of SLS printing is the ability to combine additive and subtractive manufacturing techniques. This strategy can greatly reduce CNC machining time and reduce waste material by SLS printing the rough shape, and then machining the final product. Manufacturing companies usually offer this as a service for quick-turn prototyping before moving on to large-scale production.
What Are Some of the Major Benefits of Rapid Prototyping for IoT Hardware?
As stated above, it is imperative that your IoT products go on the market faster than the competition. Rapid prototyping will increase the productivity of your IoT mechanical engineers and product designers by allowing them to design, print, and iterate in a timely manner. This also creates a more robust product that has gone through many design changes to achieve the most viable product.
Another major benefit is how rapid prototyping lowers the overall cost of the project and fits into an agile development model. By allowing engineers and designers to iterate on designs quicker, the time and money of the project will ultimately decrease. This also leads to a reduction in costly tool price changes when moving the manufacturing process to something like injection molding.
Why Rapid Prototyping Puts You Ahead
With rapid prototyping, you have peace of mind that your product is ready for the market. Since your design has gone through many iterations of design, testing, and validation, your team has already identified and fixed flaws that the product may have had. This also allows you to get immediate testing from real users who may use this product and get valuable feedback.
Product Elegance
Rapid prototyping is one of the key elements that make good products great. As product designers and mechanical engineers, we are very fortunate to have access to advanced programs and tools. As sophisticated as our workflow has become, there is still no substitute for how a product feels in the human hand. The ability to touch and interact with your prototype as you perfect the design means you won’t have to settle or wait weeks to implement improvements.
Efficiency: Cost, Ease, and Time-to-Market
At the end of the day, companies want customers to love their products. Going to market with a product that has been designed, printed, and iterated on multiple times instills confidence in the product development team and ensures an end product they can be passionate about.
In the past, this high level of polish and confidence was reserved for large firms with massive R&D budgets. Now, the barriers to entry are lower, with free software and affordable hardware readily available.
With the introduction of cost-effective 3D printing solutions, smaller companies no longer need to fear upfront tooling costs. Rapid prototyping makes it possible for you to hold in your hand what was once in your head, quickly adapt it to meet customer needs, and get it on the market fast.