
Predicting Remaining Useful Life (RUL) is one of the core benefits of the Industry 4.0 approach. Due to the rapid deployment of Internet of Things (IoT) devices, data sources for variables such as vibration, pressures, current, and temperatures are now becoming widely and readily available. This — coupled with digital maintenance records — provides insight into equipment health like never before.
The access to this data could not have come at a more opportune time. Concurrent with the explosion of new digital equipment comes two other important developments: an aging workforce and deep learning advances. In the past, predicting when equipment should be replaced relied heavily on subject matter expert input. This expertise was dependent on select individuals with highly specialized knowledge. As the workforce in the U.S. continues to age, many of these individuals are leaving the industry and creating a significant knowledge gap. Also, the advent of cheap GPUs and significantly deeper models has increased the potential for high-quality artificial intelligence options for predicting failures before it happens. Before we jump into the methodology, let’s take a look at what Remaining Useful Life (RUL) is.
What Is Remaining Useful Life (RUL)?
RUL is the length of time a machine is likely to operate before it requires repair or replacement. By taking RUL into account, engineers can schedule maintenance, optimize operating efficiency, and avoid unplanned downtime. Although nuanced, this concept is different when compared to anomaly detection. Anomaly detection could play a part in predicting remaining useful life, but it is more focused on emergent events which will rapidly degrade equipment performance. RUL focuses more on long-term asset management and is measured in terms of years rather than days.
Predictive RUL Methods
The methods used to predict RUL are significantly varied, but can be roughly sub-divided into three basic categories:
- Expert-Based Systems: This type of approach is relatively simplistic and relies heavily on human input. Essentially, this system simply compares the current data to previously observed expert-classified instances. These are human-developed rules or thresholds that are tied to a specific RUL. These rules could simply be contained in a procedure/manual or tied to a fuzzy logic output. Of all methods, this is the least exact, as the output will be essentially discrete. Additionally, it may not handle previously unanalyzed events well. It also requires a great deal of initial input from a subject matter expert.
- Physics-Based Systems: Physics-based systems are essentially hand-made mathematical models, designed to predict future degradation based on physical characteristics. Note that these models are failure mode specific. For instance, in 1962 a method was proposed for the growth of cracks based on material and variations under load. These types of models can be highly accurate but require significant expert knowledge and input.
- Machine-Learning-Based Models: Of all the methods provided here, this method is the most easily generalized and requires very little equipment expert input. It is statistically driven, meaning that a large amount of high-quality data is needed to develop the initial model. This method is further expounded upon in the next section.
Machine-Learning-Based Methods
#1: Supervised
The supervised machine learning method is likely the most intuitive, but it tends to be the most costly from a data annotation perspective. To truly be able to train a totally supervised model, one needs a massive amount of data with multiple, full-lifetime runs to be effective. Additionally, although anomaly detection and RUL are two different things, the ability to provide anomaly detection inputs into an RUL model is important. By the very definition of anomaly detection, the data is simply that, anomalous. This means even with a large cache of data, certain scenarios may not be present. To help visualize this concept, see figure 1 below.
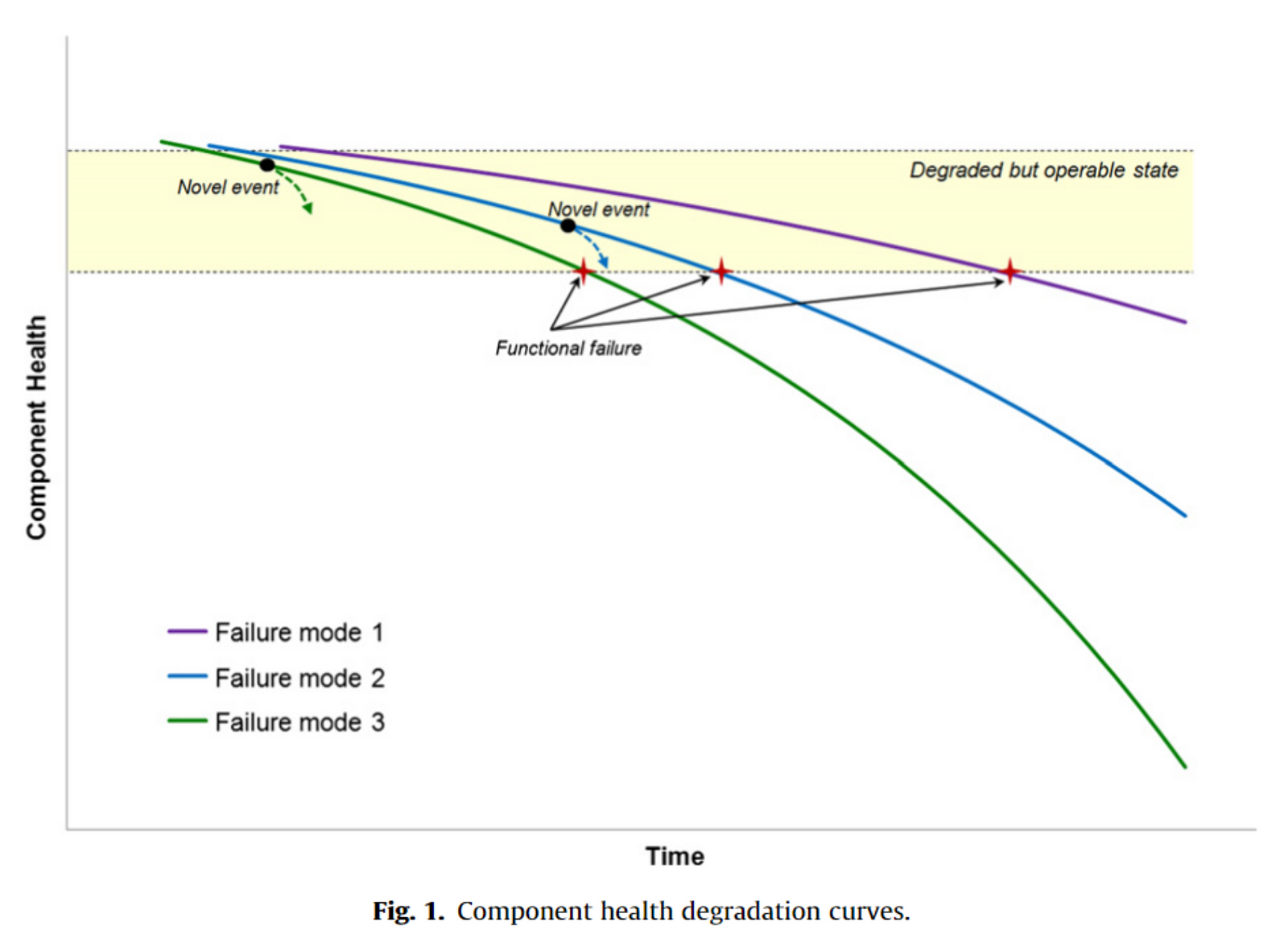
Although certain instances are solely age-related, other degradation curves are more closely tied to an event during the life of the asset. For instance, an overvoltage event in the life of a large motor may significantly change the degradation curve of the component. The model needs to be able to identify these phenomena and update the curve accordingly. There are methods for correcting for lack of data. Multiple synthetic datasets exist which can be used to augment real-world data. A supervised model can be trained on a simulation of a large pump/motor and then fine-tuned on real-world data for the specific assets in question. Ultimately, this is a time-series problem; a certain block of time from various sensors can be given to the model with the target predicted variable being the remaining life.
#2: Unsupervised
Although investigated less, fully unsupervised approaches to RUL do exist. The benefit of this approach is that no labeling is needed. In other words, data is provided straight to the model and it outputs predictions. One such example of this utilizes an Autoencoder approach. This type of model essentially outputs how “normal” data is based on previously seen data. This is coupled to create a metric termed Virtual Health Index which is then used as input to a long-term short-term memory type model to make an RUL prediction. As one can tell from the date of publication, this type of methodology is a bleeding edge. If one could use unsupervised approaches to accurately predict RUL, this would be paradigm-shifting for the field.
#3: Semi-Supervised
This method represents something of a compromise between the two options above. It allows for pre-training to occur and identifies degradation stage types prior to any supervised learning. Utilizing the C-MAPPS dataset (a standard benchmark in the field), one method was able to produce state-of-the-art results. This method was somewhat complex as it used a Restricted Boltzman machine in tandem with a long-term short-term memory model, while all the parameters were optimized through the use of a genetic algorithm. In the short term, this semi-supervised approach will likely be the model type with the best business case.
Recognizing Industry 4.0
To fully realize the benefits of Industry 4.0, RUL predictive models must be developed and implemented. The rapid deployment of IoT sensors coupled with the increasing loss of key subject matter experts mandates this development. The explosion of available data allows for accuracy previously unattainable. With proper implementation, the benefits of Industry 4.0 can provide longer asset runtimes and significantly better maintenance strategies for any company.